Industry 4.0, smart factories, and next-generation manufacturing technology are here. But, manufacturers are wondering how their manufacturing equipment will keep pace with the evolving landscape.
Industry 4.0 is in full swing. Learn how to turn this transformation into a competitive advantage with our “Manufacturing Industry Trends” white paper.
Let’s take a deep dive into the world of manufacturing equipment by learning:
- What is manufacturing equipment?
- How Industry 4.0 manufacturing equipment pushes productivity to the next level
- Real-life examples of companies putting new manufacturing technology to work
What Is Manufacturing Equipment?
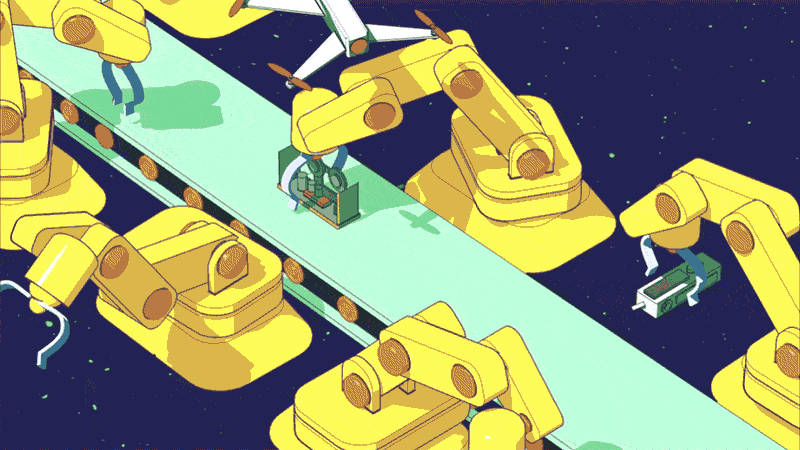
Manufacturing equipment is defined as “anything kept, furnished, or provided for a specific purpose.”
Essentially manufacturing equipment is anything that supports the function of manufacturing goods for sale by the company.
Examples of standard manufacturing equipment include:
- Machinery
- Materials
- Tools
- Technology
- Factories or plants
- Personnel equipment
With the rise of Industry 4.0, technology is becoming a must-have tool for factories of the future.
Why You Need Manufacturing Equipment
Manufacturers need dependable equipment to help them deliver on their promises to customers.
With the right equipment, manufacturing companies can:
- Create products and goods sold to customers
- Avoid mistakes in production caused by human error
- Maintain their competitive advantage over peers
- Engage their frontline workforce in other areas of the business, e.g. packaging for small business
- Reduce employee safety incidents
- Operate more sustainably
- Improve productivity and streamline processes
How To Manage Manufacturing Equipment
Manufacturing equipment needs regular management and maintenance to maximize productivity levels.
It’s natural for heavy equipment to experience wear-and-tear over the years. So, a thoughtful management strategy can help your equipment go the extra mile.
In your management strategy, it’s important to consider:
- Plan for regular machinery downtime
- Prepare for unplanned downtime and how you’ll reallocate capacity if a machine goes down unexpectedly
- Integrate new technologies that can enhance performance and productivity
- Capture performance trends by logging downtime and repairs over the equipment’s lifetime
Pro tip: Still logging manufacturing equipment maintenance by pen and paper? Mobile employee apps, like Beekeeper, can help you go digital so frontline employees can access that information right on the shop floor.
Introducing Industry 4.0 Manufacturing Equipment
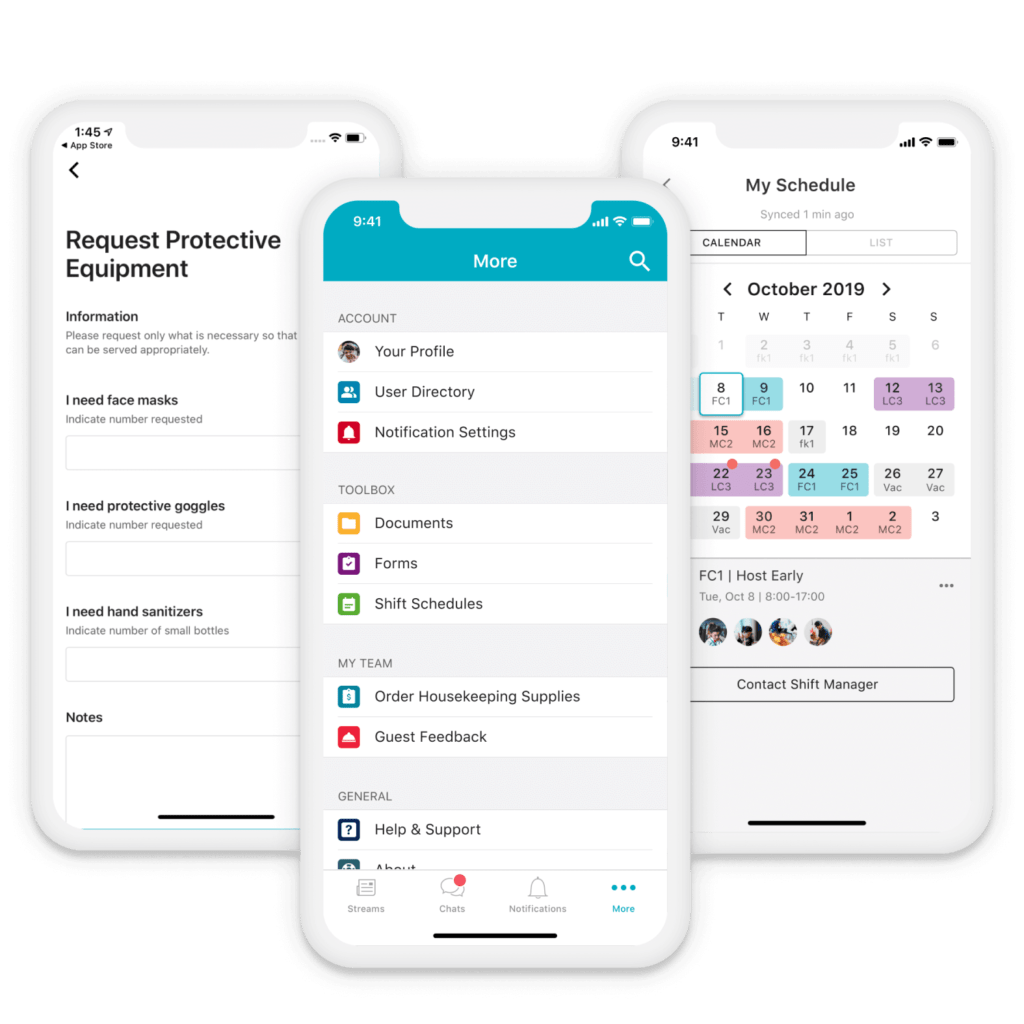
ICYMI: The global manufacturing industry is going through a serious digital transformation called Industry 4.0.
According to Epicor, Industry 4.0 is:
“A new phase in the Industrial Revolution that focuses heavily on interconnectivity, automation, machine learning, and real-time data. Industry 4.0, which encompasses IIoT and smart manufacturing, marries physical production and operations with smart digital technology, machine learning, and big data to create a more holistic and better-connected ecosystem for companies that focus on manufacturing and supply chain management.”
This focus on connectivity is driving five manufacturing trends in the industry:
- Growing adoption of robots in factories
- Increasing focus on operational excellence practices
- Integrating machine learning and AI technology
- Training and upskilling the manufacturing workforce
- Investing in frontline workforce communication platforms
Additionally, circular manufacturing economies are starting to catch on. Circular manufacturing focuses on sustainability – both for the planet and customers.
Circular manufacturing includes:
- Recovering and repurposing materials and resources
- Increasing the life of equipment and machines through predictive maintenance
- Switching to renewable energy to power factories
- Leasing equipment as part of a sharing economy
How Industry 4.0 Manufacturing Equipment Boosts Productivity
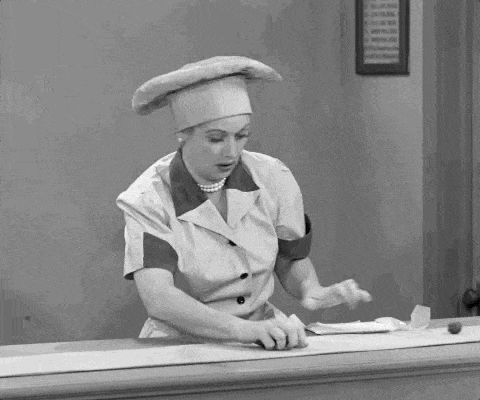
Given the COVID-19 pandemic and ensuing economic downturn, companies all over the world are looking to:
- Adopt flexible processes and practices
- Reduce expenses
- Ensure employee safety
- Boost productivity
Here are five ways Industry 4.0 manufacturing equipment can increase efficiency:
- Zero downtime. New sensor technology can provide better insight into when equipment maintenance is needed. This is referred to as predictive maintenance – and it helps eliminate disruption resulting from equipment failures.
- Around the clock production. Unlike humans, automation doesn’t sleep. With automated processes, companies can keep production going around the clock, leading to higher production volumes and faster delivery.
- Data-driven process improvements. Data gathering and analysis is a big part of Industry 4.0. As a result, companies are compiling data to optimize their processes.
- Significant waste reduction. Companies operating under a circular manufacturing mentality are focused on sustainable practices that eliminate waste.
- Produce quality products consistently. With Industry 4.0 technologies, companies can ensure reliable quality management over their products.
Companies Using Industry 4.0 Manufacturing Equipment
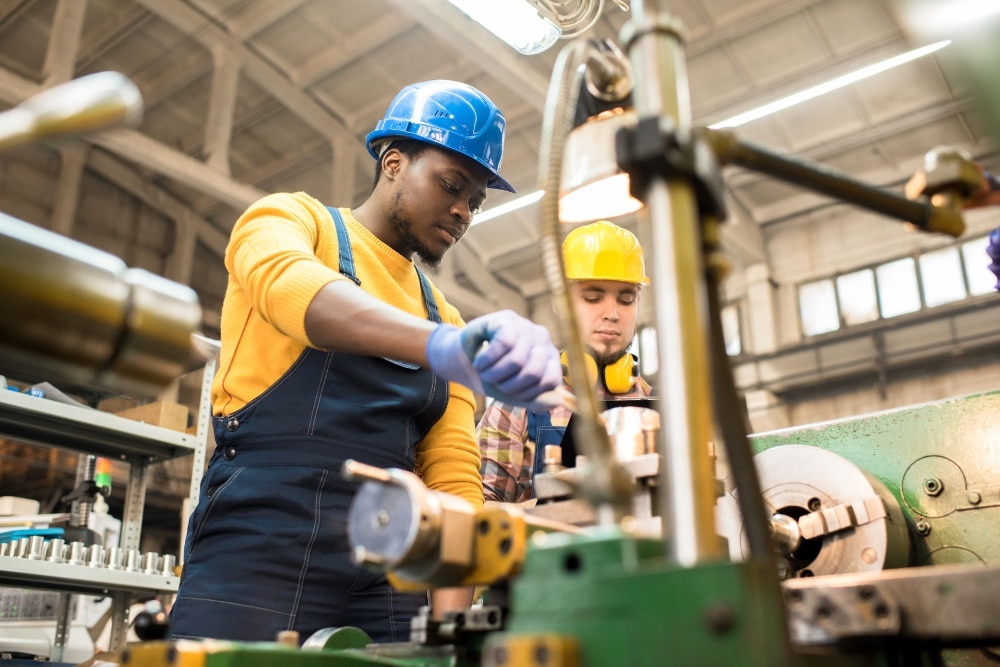
Companies that adopt Industry 4.0 manufacturing equipment can benefit from improved productivity and higher returns.
Let’s look at some examples.
Industrial Equipment Manufacturing: Ford and IRP Meat and Seafood Co.
In industrial equipment manufacturing, Ford and IRP Meat and Seafood Co. are two examples of Industry 4.0 adopters.
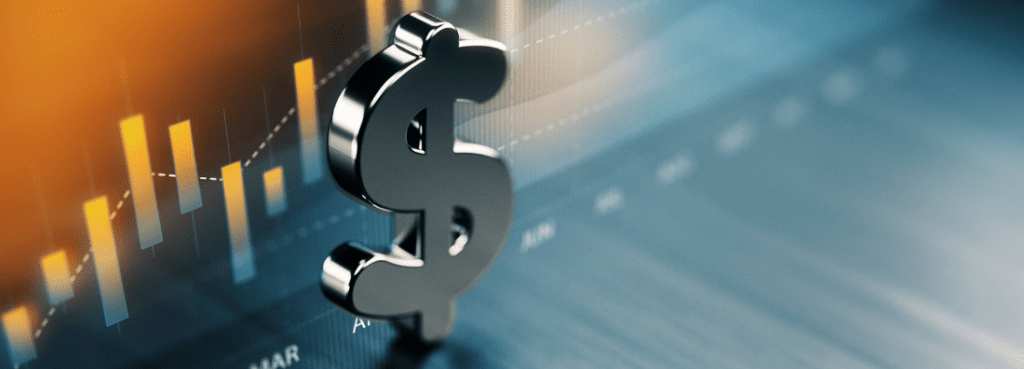
Ford’s Advanced Manufacturing Center in Redford, Michigan houses some of the company’s most innovative technology.
In the facility, Ford’s manufacturing technology experts work with equipment like:
- 3D printers
- Augmented reality
- Collaborative robots, or cobots
These next-generation manufacturing tools save the company time and money when producing high-quality vehicles.
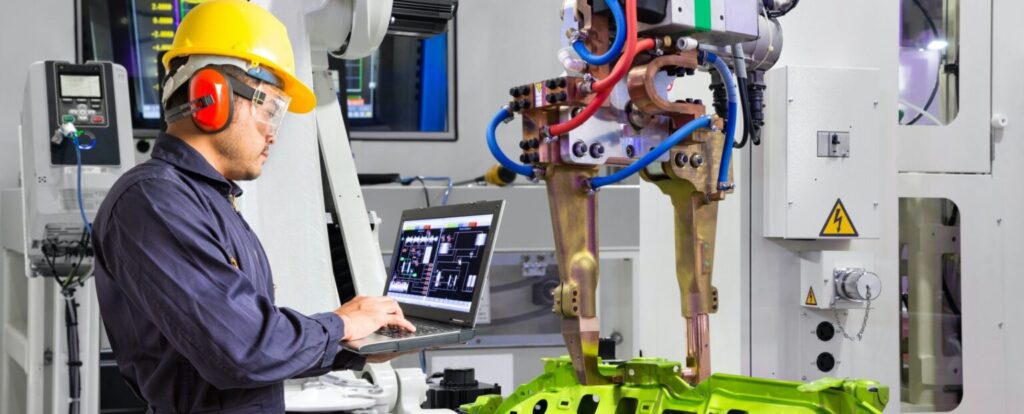
IRP Meat and Seafood Co. adopted digital employee communication technology to reach its production floor employees.
With its mobile-first Beekeeper app, IRP Meat and Seafood Co. can now:
- Connect with all employees, no matter if their front office or on the front line
- Provide better customer service with real-time communication between employee groups
- Give their employees instant access to health and safety information
Medical Equipment Manufacturing: Johnson & Johnson
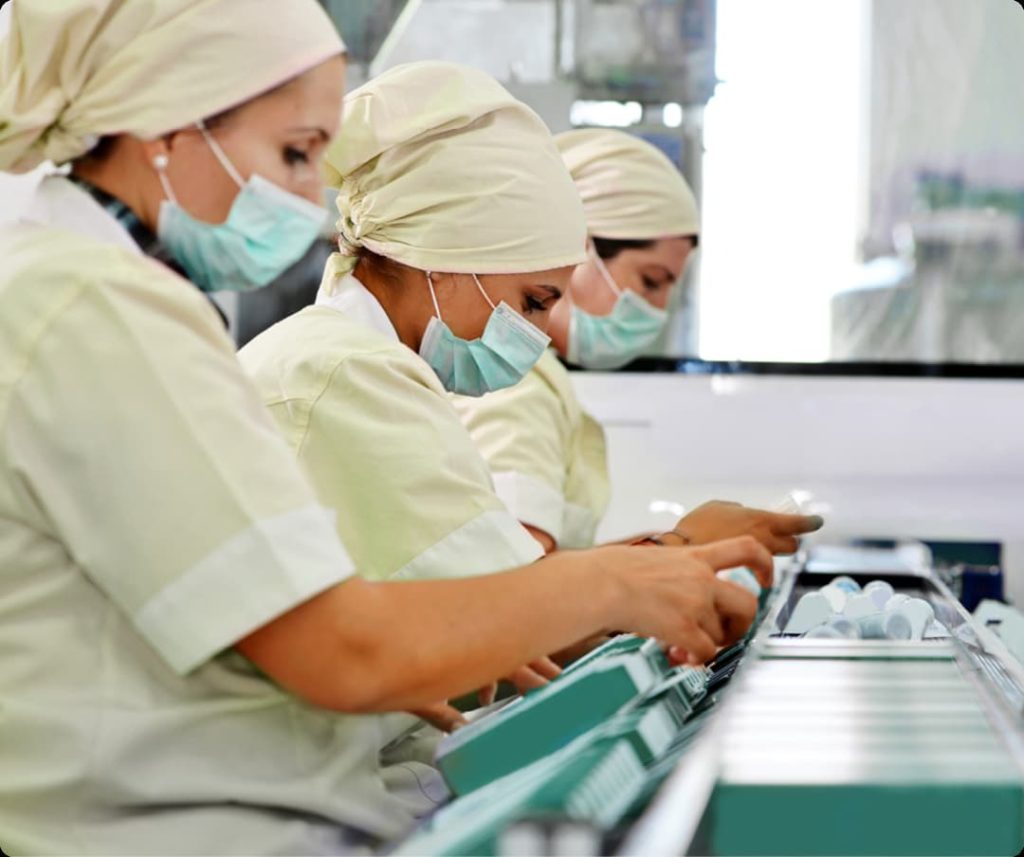
Next, Johnson & Johnson is leading the way in adopting Industry 4.0 medical equipment manufacturing tools.
Johnson & Johnson uses data and analytics to continually improve supply chain operations. With better insight into manufacturing processes, the company can identify real-time issues and better predict equipment problems before they happen.
Like Ford, Johnson & Johnson also uses cobots.
“Johnson & Johnson supply chain teams have YuMi—a collaborative robot that can do certain repetitive assembly tasks to help increase productivity and get products to consumers faster.”
Semiconductor Manufacturing Equipment: Intel
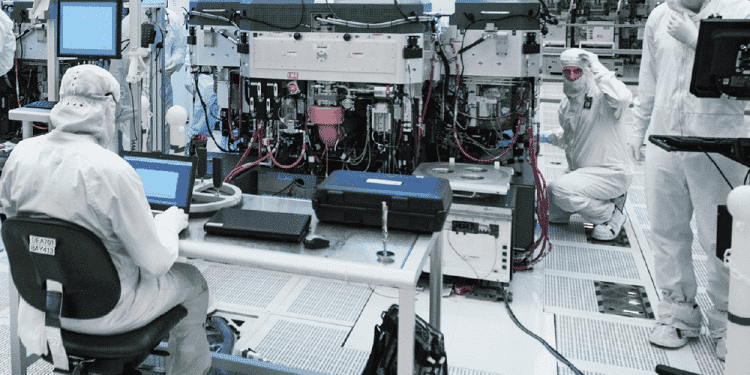
In semiconductor manufacturing equipment, Intel is using predictive maintenance techniques to manage downtime better.
Intel wanted to find a way to monitor its critical fan filter units (FFUs) more efficiently to:
- Prevent unscheduled downtime
- Reduce maintenance costs
- Create a more realists maintenance schedule
Intel formed a baseline for FFU performance using sensors and machine learning technology. Now, the company can better predict machine challenges and maintenance needs.
As a result, Intel has decreased FFU downtime by 300% and improved uptime by 97%.
Tips For Integrating Industry 4.0 Manufacturing Equipment
Navigating new manufacturing technology can be overwhelming. So, let us help.
Here are some best practices to consider in your manufacturing equipment upgrade strategy.
Upgrade Employee Tech
With Industry 4.0, employees need the ability to:
- Communicate with advanced machines and other tools
- Connect with fellow employees and their managers
- Access on-the-go information while on the production floor
This is why mobile-friendly employee technology is key when upgrading your manufacturing equipment.
Benefits of mobile communication in manufacturing include:
- Provide instant access to essential information employees need to do their jobs well
- Create a transparent work environment by using open feedback loops
- Boost team collaboration and employee morale
- Promote workplace safety with access to real-time regulatory updates
- Communicate instantly
Keep Workplace Safety At The Forefront of Your Strategy
The manufacturing industry ranks third for on-the-job incidents, with an average of 400,000 nonfatal injuries a year.
The adoption of Industry 4.0 tools, like robots, automation, and data gathering, improve workplace safety. For example:
- Robots handle the more dangerous tasks
- Digital communications give access to health and safety protocols, reducing safety costs on average $400,000 per year
- Predictive maintenance can prevent hazardous equipment failures
Go Green
Customers, investors, employees, and communities are calling for more environmentally conscious manufacturing processes.
Here are four ways manufacturing companies can go green:
- Save energy and reduce waste with circular manufacturing
- Create safer working environments with automated tools, AI, IoT, and cobots
- Digitize employee communications
- Integrate eco-friendly products
Most Frequently Asked Questions
What are examples of manufacturing equipment?
Examples of standard manufacturing equipment include:
- Machinery
- Materials
- Tools
- Technology
- Factories or plants
- Personnel equipment
What is manufacturing equipment?
Manufacturing equipment is defined as “anything kept, furnished, or provided for a specific purpose.” Essentially, manufacturing equipment is anything that supports the function of manufacturing goods for sale by the company.
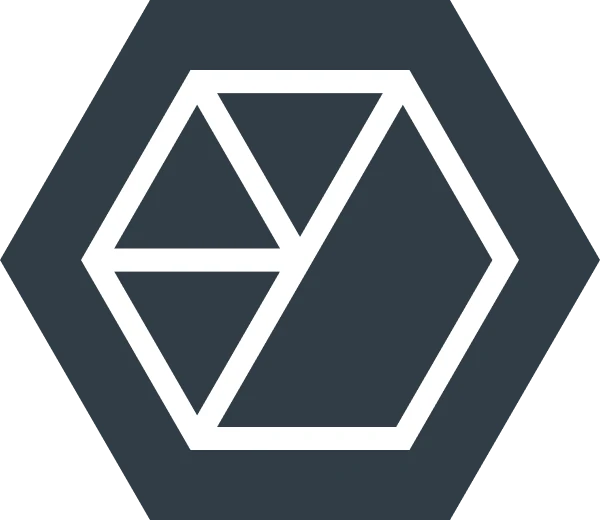
About the author
Beekeeper
We make frontline lives easier, work safer, and teams more connected so businesses can reach new heights. At Beekeeper, we’re dedicated to making frontline lives easier by connecting workers with the tools, support, and information they need to feel valued, do their best work, and drive the business forward.