Top 10 Manufacturing Trends for 2023
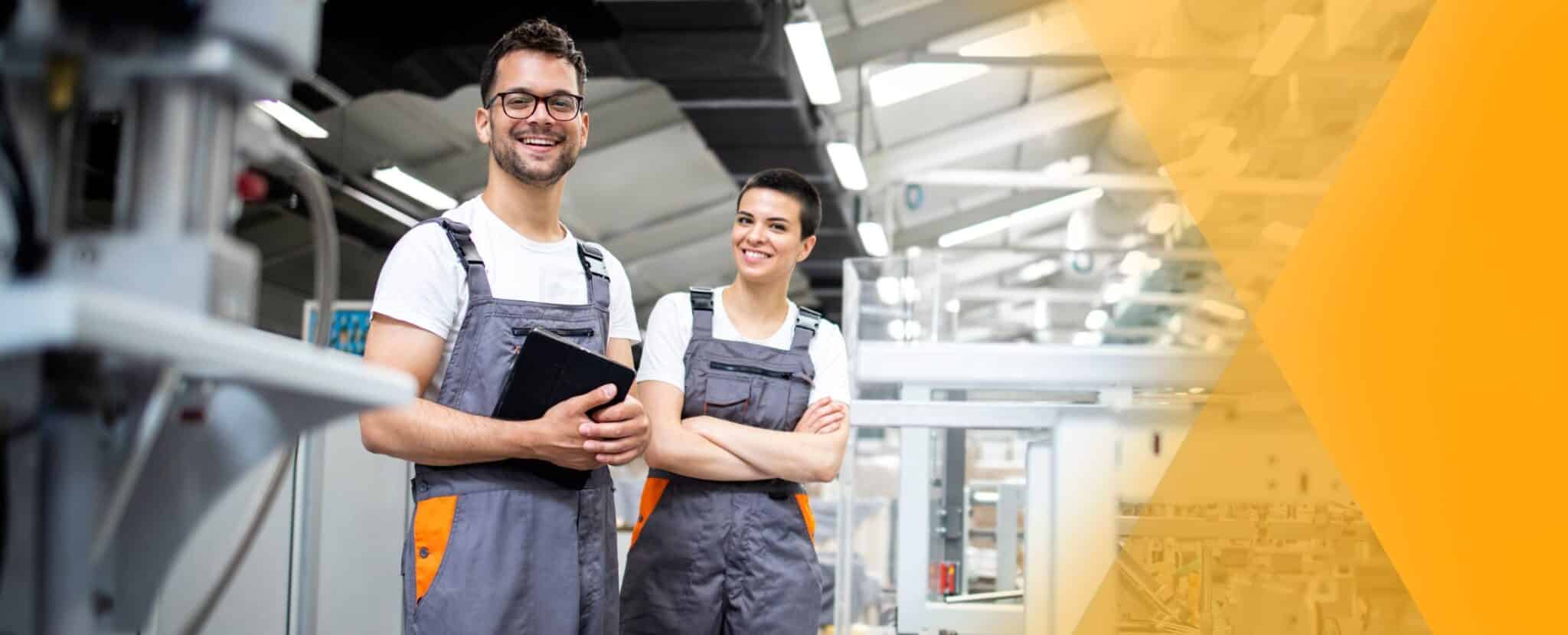
Table of contents
- Trend #1: Increased Output Amidst a Decline in Labor Force
- Trend #2: Continued Efforts to Solve and Manage Supply Chain Issues
- Trend #3: Building a Resilient Workforce
- Trend #4: Automation and Robotics are Redefining Manufacturing Worker Roles
- Trend #5: More Focus on Carbon Neutrality
- Trend #6: Increased Importance of HR in Attracting and Retaining Manufacturing Workers
- Trend #7: Employees Participating in Continuous Learning and Improving Skills
- Trend #8: Industry 4.0 and Smart Factories
- Trend #9: Reshoring
- Trend #10: Two-Way Mobile Communication
- Manufacturing Trends Frequently Asked Questions
This year has proved to be both dynamic and disruptive for the manufacturing industry and 2023 shows no sign of slowing down.
Manufacturers are still recovering from the impact of the coronavirus pandemic and face challenges like:
There is a clear divide between what today’s mobile, deskless workforce needs and the company processes built to support them. That’s why workers are quitting in droves, with global average turnover rates reaching +40% across hospitality, manufacturing, healthcare, construction, and retail.
- The labor shortage
- The skills gap
- Workers’ roles with the rise of automation
- Retaining and attracting new employees
We’ll be looking at the must-know manufacturing trends that will shape manufacturing industries in 2023 and how companies can better prepare for the future.
Download Our 2023 Frontline Trends Report: Effects of the Labor Shortage
Trend #1: Increased Output Amidst a Decline in Labor Force
Over the past decade, we’ve seen an overall decline in the number of manufacturing jobs.
According to the U.S. Bureau of Labor Statistics, manufacturing is projected to shed over half a million jobs between 2012-2022. This 0.5% decline is still far slower than the 2.4% rate of the previous decade.
Moving into 2023, manufacturing companies will have to keep up with increasing demand while retaining their skilled workers.
For frontline industries like manufacturing, employee retention is critical for keeping up with the demand in output.
Trend #2: Continued Efforts to Solve and Manage Supply Chain Issues
Given the global shortage of materials and high energy costs, bottlenecks and delays are expected to last into 2023.
At the same time, consumer expectations remain as high as ever so manufacturers have to develop workarounds to satisfy consumer demand.
Having effective communication strategies in place can help mitigate the effects of disruptions. Effective workplace communication ensures that everyone is on the same page and is working towards the same goal.
For manufacturing companies with a distributed frontline workforce, mobile platforms like Beekeeper allow employees to communicate in real time across different locations.
Trend #3: Building a Resilient Workforce
The U.S. is expected to have 2.1 million unfilled manufacturing jobs by 2030, according to Deloitte. This worker shortage is partly responsible for slowing down the growth and speed of operations.
Diversifying the manufacturing workforce is a global trend. In India, Daimler India Commercial Vehicles launched an initiative to hire more women until they make up 20% of their motor vehicle workforce.
Here’s what Beekeeper’s Senior Account Executive RJ Bisaha had to say about what he’s noticed about hiring in manufacturing:
Many manufacturers are going outside the box to source new talent. Companies are reaching out to and partnering with employment programs designed to help veterans, women, refugees, and other underserved populations.”
In 2023, we’ll be seeing more companies look for ways to diversify their workforce in order to make their operations more resilient.
Trend #4: Automation and Robotics are Redefining Manufacturing Worker Roles
Automation in the manufacturing industry isn’t a new phenomenon. But manufacturing companies are investing more money than ever into automated solutions for their operations. This is particularly true for the agricultural and food manufacturing industry. In fact, the global agricultural robotics market will be worth $6.7 billion by 2032.
This focus on automation and robotics is shifting the structure and distribution of labor in manufacturing. Companies have to re-evaluate how to make the best use of their workforce.
Trend #5: More Focus on Carbon Neutrality
Climate change has become an urgent priority for the manufacturing industry. Manufacturing accounts for about one-third of global greenhouse emissions, which is driving companies to rethink their operations model and move towards low-carbon or carbon-neutral manufacturing systems.
Governments are taking big strides towards sustainability, investing trillions of dollars into combating climate change. These policies will require manufacturing to transform end-to-end operations, from designing and delivering products to factory models.
This overhaul of manufacturing operations will also prompt a shift in how companies approach internal communication.
Trend #6: Increased Importance of HR in Attracting and Retaining Manufacturing Workers
Part of dealing with the labor shortage and skills gap in manufacturing involves attracting and retaining younger workers and those re-entering the workforce post-pandemic.
Older workers who have built expertise and hands-on experience are retiring. At the same time, automation and robotics are creating demand for new roles and skills in manufacturing.
Manufacturing companies need to attract new workers and boost employee retention to solve the skills gap and keep up with demand. Moving into 2023, we’ll see HR departments rethink their approach to the employee life cycle.
Trend #7: Employees Participating in Continuous Learning and Improving Skills
Learning and skills development doesn’t stop on the last day of onboarding. Continuous learning is one of the key factors in employee retention, especially for younger workers.
One way to make continuous learning sustainable for existing employees is to offer mobile training programs on a platform like Beekeeper.
With Beekeeper, managers can develop an effective manufacturing training program that employees can complete on their mobile devices. Beekeeper’s inline translation tool ensures that every manufacturing worker has equal access to participate.
Trend #8: Industry 4.0 and Smart Factories
This trend involves the integration of advanced technologies such as the Internet of Things (IoT), artificial intelligence (AI), and robotics to create highly efficient and flexible production systems.
Smart factories use sensors to gather data on every aspect of the production process, from raw materials to finished products. This data is then analyzed by AI algorithms to identify patterns and optimize production in real-time, allowing for more efficient use of resources, reduced waste, and improved quality control.
By automating dangerous or repetitive tasks, workers can be freed up to focus on more complex and value-added activities. This reduces the risk of accidents and injuries, while also improving job satisfaction and retention.
Trend #9: Reshoring
Reshoring is a manufacturing trend that involves bringing production back to the domestic market from offshore locations. Rising costs of raw materials and offshore production, increased wages overseas, and the desire to improve supply chain resilience are all driving this trend.
By restoring production, companies can reduce their dependence on foreign suppliers, improve their ability to respond to unexpected events, and meet environmental standards more easily.
Trend #10: Two-Way Mobile Communication
One of the communication trends we’re seeing at Beekeeper is more manufacturing companies switching to two-way mobile communication as their main internal communication strategy. Two-way mobile communication allows manufacturing companies to stay in touch with their workforce in real-time, meaning that employees can receive updates, alerts, and other important information on their mobile devices, and can respond to these messages instantly.
This type of communication is particularly useful in manufacturing environments where employees may be working in different locations or on different shifts. At Beekeeper, we’ve seen how two-way mobile communication has improved employee engagement, boosted productivity, and helped create a positive and safe workplace culture for manufacturing organizations.
In fact, we’d argue that two-way mobile communication is essential for Frontline Success and it’s a trend we expect to continue to grow throughout 2023 and beyond.
Manufacturing Trends Frequently Asked Questions
Now it’s time for the lightning round, aka answering the most frequently asked questions about what’s coming up for the manufacturing industry.
What are the main drivers behind the adoption of these manufacturing trends?
- Technological advancements: The development of new technologies such as automation, artificial intelligence, and the Internet of Things (IoT) has revolutionized the manufacturing process
- Consumer demand: Consumers are increasingly demanding personalized and high-quality products that can be delivered quickly, leading manufacturers to adopt new technologies and processes to meet these demands
- Global competition: With the rise of globalization, manufacturers are facing increased competition from around the world
- Environmental concerns: There is growing concern about the impact of manufacturing on the environment, so more manufacturers are adopting sustainable practices to reduce their environmental impact
How can small and medium-sized enterprises (SMEs) implement these trends?
Yes! Here’s how:
- Start with a plan that outlines goals, objectives, and resources available
- Invest in technology such as automation, IoT, cloud computing, and mobile communication platforms
- Implement lean manufacturing to reduce waste, improve efficiency, and optimize production processes
- Collaborate with suppliers to implement new industrial manufacturing trends
- Train employees to use new technologies and processes properly
- Monitor and adapt processes and strategies as needed
Are there any potential risks or challenges associated with these trends?
Some of these risks and challenges could include:
- Cost: Implementing new technologies or processes can be expensive
- Complexity: Some manufacturing industry trends can be complex and may require specialized expertise to implement
- Resistance to Change: Leadership teams and employees may resist changes to their work processes
- Supply Chain Disruptions: Changes in manufacturing processes can affect the supply chain, and manufacturers may need to work closely with suppliers to mitigate risks
- Legal and Regulatory Issues: Implementing new technologies or processes may require compliance with legal and regulatory requirements, which can be complex and time-consuming
How can manufacturers prepare their workforce for the adoption of new technologies?
- A change management plan that includes clear communication, stakeholder engagement, and a phased implementation plan
- Communication with employees about the benefits of new technologies and how the new technologies will impact their work
- Enabling collaboration between employees and departments to share knowledge and best practices
- Training and upskilling using training programs, workshops, and online courses
What role does government support play in promoting these trends in manufacturing?
Government support can play an important role in promoting manufacturing trends in several ways:
- Funding and investment to manufacturing industries to help them develop new technologies, processes, and products
- Investing in infrastructure development, such as roads, railways, and ports to reduce transportation costs and increase access to global markets
- Create a regulatory framework, which includes policies and regulations that promote sustainability, safety, and quality standards, as well as incentives for companies that adopt sustainable practices
- Develop trade policies that promote manufacturing trends, such as free trade agreements and export incentives
- Support workforce development initiatives, such as vocational training programs and apprenticeships
Get More In-Depth Insight Into Manufacturing Trends With Our 2023 Frontline Trends Report
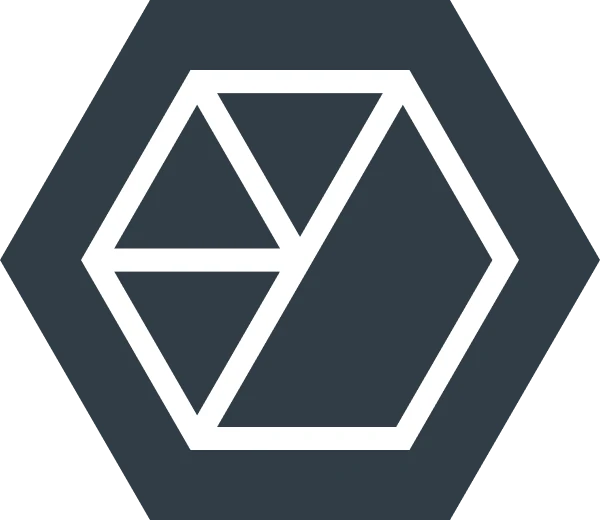
About the author
Beekeeper
We make frontline lives easier, work safer, and teams more connected so businesses can reach new heights. At Beekeeper, we’re dedicated to making frontline lives easier by connecting workers with the tools, support, and information they need to feel valued, do their best work, and drive the business forward.