As manufacturing companies look for ways to invest in their future, the obvious choice is to go all-in on digital transformation to keep up with the competition. But along with a digital strategy, companies also need to invest in optimizing their workforce. And the best way to do that is with a strategic, well-thought-out manufacturing training program.
Manufacturing has a widening skills gap and a workforce that isn’t fully prepared for Industry 4.0.
Create a safety-first manufacturing culture through digital enablement. Get the safety checklist here.
According to McKinsey, the need for workers with a new set of technological skills is predicted to grow by 50%. There will also be a 30% increase in demand for soft skills as jobs shift towards more cognitive roles.
Designing an internal training program for your manufacturing workforce can fulfill all of those needs, empower workers, and close that skills gap. It’s a must-have strategy for companies to keep up and stay competitive in the changing world of manufacturing.
What Are Manufacturing Training Programs?
A manufacturing training program is a business strategy to give employees new skills to meet the needs of their workplace. Companies create a curriculum so workers can acquire the knowledge they need to excel in their jobs, give productivity a boost, create a safer work environment, and stay current with the technological advances in manufacturing.
Why Are Manufacturing Training Programs Important?
For decades, the manufacturing industry was largely conservative in its approach, and change happened slowly, if at all. Now, the industry is making up for lost time. There is a surge of interest in digital transformation, but the skills of the workforce are often stuck in the past. Manufacturing training programs give both employees and a company the resources to perform at a higher level. Here are the top reasons why companies need a manufacturing training program.
- Onboarding: It takes an average of 65 hours to get new employees up to speed on what they need to know. Creating a dedicated digital training program at onboarding maximizes productivity by getting employees up and running faster.
Pro tip: give new hires a training buddy so they’ve got a personal mentor from day one.
- Quality management: When an entire workforce knows exactly how to perform tasks, and they have mobile collaboration tools to share knowledge, product quality improves.
- Safety: Safety is one of the most important reasons companies need a manufacturing training program. With 400,000 workplace injuries a year, manufacturing has the third highest safety incident rate. When workers have proper instruction on safety protocols and equipment handling, accident rates can drop dramatically.
- Customer service: In the competitive manufacturing landscape, companies with a skilled workforce are more efficient and more productive. This reduces manufacturing overhead and waste, which enables a company to deliver products faster and better, driving customer loyalty and attracting new business.
- Employee engagement: Manufacturing training programs empower employees by giving them the potential to earn more and grow in their careers which ultimately leads to higher engagement.
5 Steps for Implementing a Manufacturing Training Program
Like any business strategy, implementing a manufacturing training program needs to be mapped out before it’s rolled out. Here are the five steps companies should follow to get a successful training program going.
1. Design the Training Program
Manufacturing training programs are not one-size-fits-all. Companies need a program that supports their specific operation and goals.
To create a training course, companies must first:
- Identify who needs to be trained and for what tasks and skills?
- Map out company goals
- Set training objectives
- Determine KPIs to measure success
Training programs should cover all of the skills your workforce needs in order to function in your facility. But not every worker needs to have every skill. Map out workforce journeys so you know which workers need which skills.
Companies should also make sure to integrate lean manufacturing training principles into their learning program so every role in a company is contributing to a lean operation that is continually improving workflows, boosting performance, and reducing waste.
2. Develop the Curriculum and Method of Learning
Once you know who you’ll be training and what you’ll be training them to do, the next step is to create the curriculum and determine how to deliver the information.
Start with the materials. Companies can create their own training documents, produce short videos, or curate materials from outside resources. Then, determine how long the training will last until the final “exam” and organize the materials accordingly.
Next, choose a method of learning. If you don’t already have one, find a mobile productivity tool so every worker can participate in training on their mobile device. Supplement that with in-person training for hands-on learning, too.
Pro tips:
- Keep it simple. These are full-time workers who need small, digestible chunks of information that they can process on the go. Break up long, complex material into smaller bits that are easier to process. Create a set number of lessons and have a designated duration time for the training program.
- Find an external partner. Find a local vocational school who offers coursework in the areas where you want to improve training. Partner with them to bring their instructors in house, or send your workers to the school.
- Incorporate technology. Use emerging tech, like virtual reality, to simulate workflows and make learning more engaging.
3. Implement the Program
Run a pilot program of your training program to find any areas you want to improve before rolling it out to the rest of your workforce. Then, schedule the training and sign workers up for sessions. Find mentors from your management team who can assist and offer guidance to workers in training.
4. Document the training
Once you’ve created your manufacturing training programs, document them. These will serve as your guides for employees who go through subsequent training sessions. Create an SOP for each skill track. Make it available on your company’s mobile collaboration tool so employees can refer to them. Update these documents as the training evolves.
5. Regularly evaluate and improve the program
Like any part of your operation, training programs need to be regularly reviewed, evaluated, and improved. Manufacturing is constantly evolving, thanks to Industry 4.0 and emerging technology. Companies need to make sure their training keeps pace with those changes in order to stay competitive.
Why a Mobile Productivity Solution Is the Ideal Manufacturing Training Solution
A mobile productivity tool, like Beekeeper, is the perfect solution for training a frontline manufacturing workforce. A mobile-first solution can help you get the most out of a training program.
Here are just a few advantages of a mobile productivity tool:
- Feedback. With two-way communication, a mobile tool allows workers to give feedback on training programs so managers can continually improve and refine content and delivery.
- Document library. A mobile app can store training materials in one centralized location so workers can access them when they need.
- Inline translation. Choose a mobile tool that has translation features that allow every worker equal access to participate in a manufacturing training program.
- LMS integration. A mobile tool can integrate with learning management systems. For example, Beekeeper integrates Coursepath for employee training opportunities for frontline workforces.
As digital transformation continues to push manufacturing into a new era, a well-skilled workforce is critical to a company’s success. It’s up to manufacturers to provide their employees with the training they need to stay competitive and build a workforce for tomorrow.
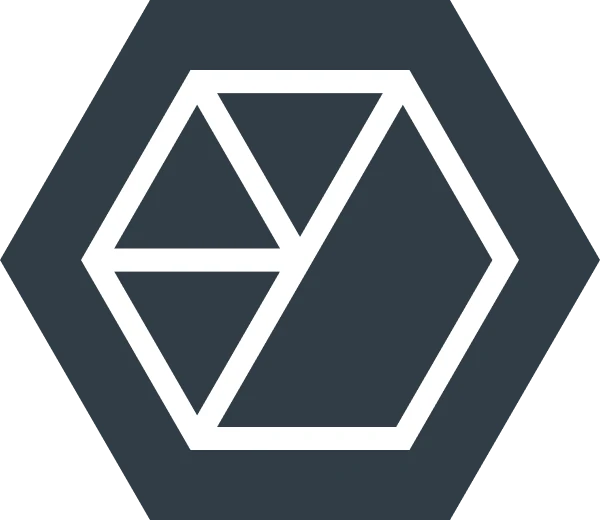
About the author
Beekeeper
We make frontline lives easier, work safer, and teams more connected so businesses can reach new heights. At Beekeeper, we’re dedicated to making frontline lives easier by connecting workers with the tools, support, and information they need to feel valued, do their best work, and drive the business forward.