Reduce Maintenance Cost: A Guide to Maintenance Management
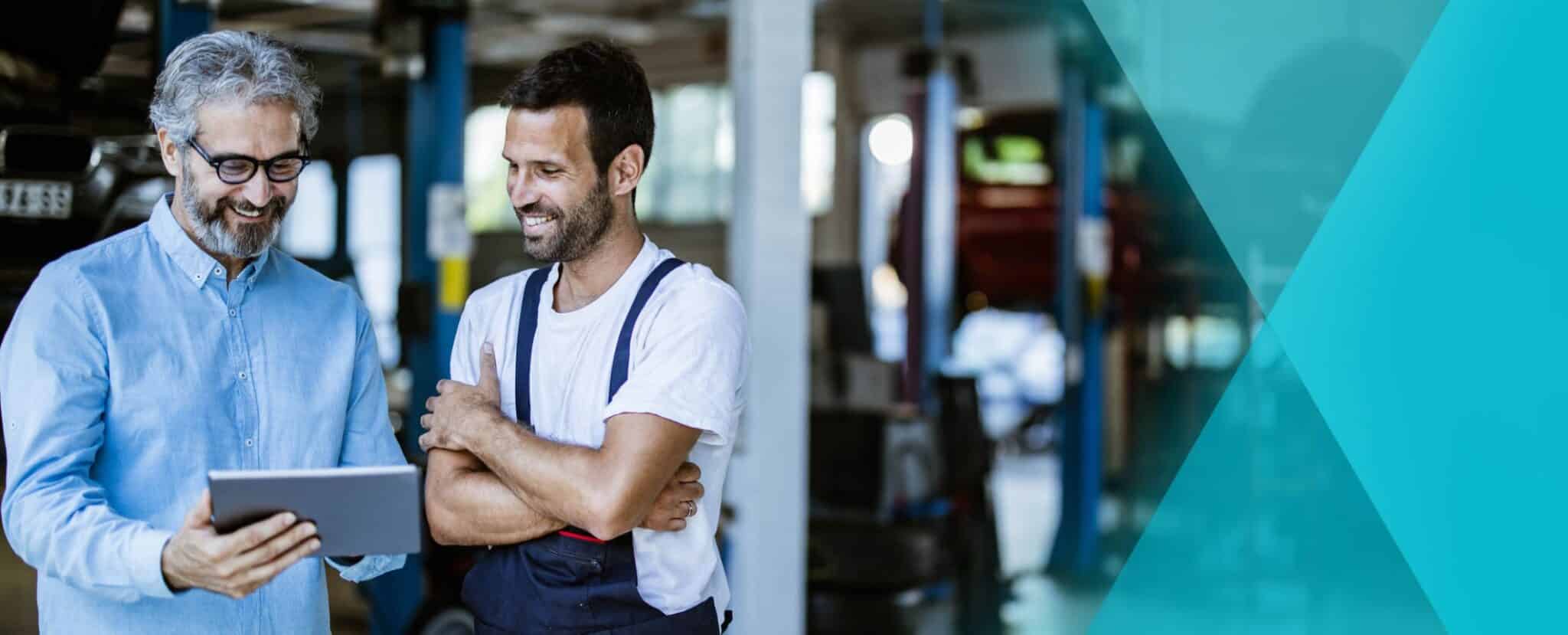
The cost of doing business right now is higher than ever. Companies are still recovering from the pandemic, struggling with supply chains and the expense of materials, are short-staffed, and operating during inflation. Everyone’s trying to cut back. There’s one strategy that businesses often overlook but can help save money: to reduce maintenance costs for every asset.
Maximize Uptime. Minimize Downtime. Boost Your Maintenance Management Processes Today
Understanding Maintenance Costs
Most companies have assets that help them run operations. And those assets require regular maintenance to maximize their productivity. But taking the wrong approach to managing equipment can create unnecessary expenses and companies need to find better ways how to reduce maintenance cost expenditures.
What Are Maintenance Costs?
Maintenance costs are the total amount of money spent inspecting, repairing, and tending to equipment and assets in a company. Whether it’s manufacturing equipment or computer hardware, assets are an investment that requires regular oversight to ensure they’re functioning properly.
The Impact of Maintenance Costs on a Business
Maintenance management is a normal business operating expense. But often, companies go over budget simply because they’re not using the most efficient methods. The result?
Companies spend a collective $222 billion on equipment maintenance every year.
Why are costs so high?
- More than 50% of companies are using a reactive maintenance approach to taking care of their equipment. That means they wait until there’s a problem or until a machine breaks down to take care of their assets. The costs of replacement are much higher than routine maintenance.
- When equipment stops working, it has to be taken out of operation to fix which creates unplanned downtime: the period that a machine is offline and work is stopped and employees are paid for the time they are not able to work.
- Many companies still rely on pen and paper to keep track of equipment maintenance. But that information is often kept in one place and not readily accessible by those who need it. It’s inefficient, things get missed, and errors occur. Digitally logging maintenance reports is a more accurate, accessible solution for an effective maintenance plan.
Strategies To Reduce Cost of Maintenance Management
When figuring out how to reduce equipment maintenance costs, there are different types of programs that might be a more economical decision for your company.
Prioritize equipment maintenance based on the amount of upkeep each asset requires and put them into one of three categories: critical, semi-critical, and non-critical. This is a more cost-effective approach to maintenance management than giving every machine the same level of service when some might not need it.
Then, select a strategy that works best for your business and the one that can reduce the cost of maintenance.
Note: One study found that companies that used preventive or predictive maintenance experienced 52.7% less unplanned downtime and had 78% fewer equipment defects than those that used reactive maintenance.
Preventive Maintenance
The first approach to equipment upkeep is preventive maintenance.
What is Preventive Maintenance?
Preventive maintenance is regularly scheduled equipment inspections in order to test the function and operability and catch any small issues and make minor repairs.
Benefits of Preventive Maintenance
Preventive maintenance is a straightforward approach to equipment management.
Benefits include:
- Reduction in unexpected malfunctions and unplanned equipment downtime
- Schedules are planned ahead of time and allow for planned downtime
- Minimize big repair expenses
- Increase workplace safety
- Limit workflow disruptions to maximize productivity
- Boost equipment lifespan
Implementing a Preventive Maintenance Program
To create a preventive maintenance program there are certain logistics to include.
- Create a prioritized list of assets requiring maintenance and inspections
- Establish the personnel who will be doing the work
- Create a maintenance schedule for each asset
- Have a document, like an SOP, that outlines the proper procedure for the inspection of each asset
- Train employees on how to do the maintenance and make sure they have access to the maintenance manual
The training of employees is especially critical for both effective maintenance and the productivity of teams. One of the top frontline trends right now is retaining workers during the ongoing labor shortage. When bringing in new maintenance tools, be sure to train your team and promote them from within.
Pro tip: Use a mobile-first, frontline success system for a cloud-based approach to maintenance management. Maintenance teams can log their work, access maintenance procedures, and report safety hazards all from one system. The tool can also be used to upskill frontline workers on new maintenance systems and tech!
Predictive Maintenance
Predictive maintenance takes a data-driven approach to understand when to inspect assets.
What is Predictive Maintenance?
Predictive maintenance is the ability to monitor equipment and collect data to detect any irregularities in the function that might be a red flag.
It tracks historic trends in operation and compares them to current patterns to predict failure. While once done with pen and paper, predictive maintenance is now made possible by the Internet of Things and AI. Sensors on machines can track functionality, like if the temperature is getting too hot on a machine, and alert maintenance teams when there is an issue.
Benefits of Predictive Maintenance
Inspecting equipment based on data and analytics delivers greater accuracy to a maintenance program
- Machines can keep operating during predictive maintenance for higher productivity
- Reduce the cost of maintenance management by 25%
- Catches issues when they happen, before they grow into bigger problems
- Supports safety compliance and reporting
- Longer equipment lifespan
Implementing a Predictive Maintenance Program
A predictive maintenance system requires new tools and more training for maintenance teams. But the ROIs are worth it. Here are the basic steps to implementing a predictive maintenance program:
- Review equipment and determine which assets are critical and require the most maintenance time and are the most expensive to operate and repair.
- Affix sensors to that equipment.
- Set parameters for function: determine data to collect to know when machines operate outside of them.
- Train staff in predictive maintenance programs and related technology, like AI
Bigger companies might have the resources to create a digital factory in which every asset is connected. Smaller companies can begin predictive maintenance machine by machine.
Condition-Based Maintenance
A hyper-focused, more immediate form of predictive maintenance is condition-based maintenance.
What is Condition-Based Maintenance?
Condition-based maintenance (CBM) is the real-time monitoring of how the asset is performing based on specific operational functions like temperature monitoring with infrared sensors, vibration analysis, acoustic monitoring, and data collection through sensors.
Think of how an electrocardiogram (EKG) works: monitors are placed on the human chest to track the rhythms and electrical system of the heart to detect irregularities in real-time. Condition-based monitoring is similar but with sensors attached all the time to catch any changes in function almost immediately.
Benefits of Condition-Based Maintenance
- CBM can happen while equipment is in operation, reducing downtime disruption and related costs
- Extends the lifespan of assets
- Optimizes maintenance schedules by notifying teams exactly when maintenance or repair is needed.
- Can detect specific parts that need attention
- Corrective actions are taken to make repairs long before failure can happen
- Fewer equipment failures for a safer workplace
Implementing a Condition-Based Maintenance Program
While CBM requires a higher level of software and technology, it is worth the investment for some companies.
- Select the critical assets (if not all of them) to place on the CBM plan
- Set a baseline for function so sensors know what irregular patterns to look for
- Train maintenance teams on skills needed to manage digital maintenance
- Equip teams with mobile communication tools to receive alerts from the sensors directly on their mobile device
Regardless of which strategy fits best, digital work management (DWM) should be the foundation of any maintenance program. That means leveraging technology to plan, schedule, and execute a maintenance management system. According to McKinsey, using digital solutions can reduce maintenance costs by 15%-30%. This is a result of several ROIs, like creating a safer workspace with fewer incidents, higher productivity, and less unplanned downtime.
Streamlining Maintenance Operations
Most companies have multiple assets to track. The best way to make maintenance cost-effective is to streamline the process instead of handling each asset individually. Use a computerized maintenance management system (CMMS), software that can be used for scheduling, issuing, and receiving work tickets, updating equipment status, and tracking all maintenance-related information.
Pro tip: Integrate your CMMS with your mobile-first, frontline success system so frontline maintenance teams can manage work tickets, report on maintenance activities, and remotely access equipment data all through one tool.
Centralized Data Management
With a CMMS, all Information can be consolidated and centralized. All maintenance management information and data funnel through a single system where it can be easily accessed by technicians. Digital inspection checklists can be created and stored on the system so all equipment status reports are immediately available.
Automation of Maintenance Processes
A digital solution can help automate the actual equipment maintenance diagnostics (like sensors tracking equipment instead of human inspections.) But it can also automate the logistics of maintenance, like scheduling and work tickets, part ordering, and technician communication. This reduces the chance of error and frees up workers to focus on value-added tasks rather than spending too much time on the mundane, repetitive tasks of maintenance management.
Outsourcing Maintenance Services
For some companies, the best option to reduce the cost of maintenance management might be to outsource the responsibility to a business that specializes in this work. They’ll track your equipment remotely and send technicians out when a problem is detected (for preventive and condition-based maintenance) or when it’s time (preventive maintenance programs.) This can save companies on the cost of salaries for on-site maintenance personnel, especially for smaller operations that don’t need a full-time team.
The Importance of Employee Training and Involvement
A mistake companies often make is taking a top-down approach to strategy development when they’re trying to achieve better results.
The Role of Employee Training in Reducing Maintenance Costs
The cost of poor communication in business is about $420,000 for a smaller company of 100 employees or less.
Pair that with the cost of a bad maintenance strategy, like reactive maintenance, and companies stand to lose a lot of money. When communication is a priority, and companies make sure that maintenance teams have the right information, training, and skills to handle the upkeep of equipment, the process is faster, safer, and has fewer, if any, errors.
Employee Involvement in Maintenance Operations
Maintenance teams are frontline workers, a demographic that makes up 80% of the world’s workforce. They are the hands-on team that performs the work and knows the step-by-step procedures for proper inspection and repairs. Their involvement and input in developing maintenance operation strategies can help accurately define the processes to reduce maintenance cost expenses.
Leaders should supply their maintenance teams with frontline success tools: a two-way communication and collaboration platform that allows workers to supply feedback and input. The ability to contribute engages frontline teams, makes them feel included, and empowers them with access to tools and data to be more productive. And that all leads to better work, lower costs, and higher profit margins.
Maintenance is a necessary part of business operations and expenses. But waiting until there’s a problem can set off a cascade of other problems. Companies should create a deliberate strategy for upkeep and inspections to reduce maintenance costs for their equipment inventory.
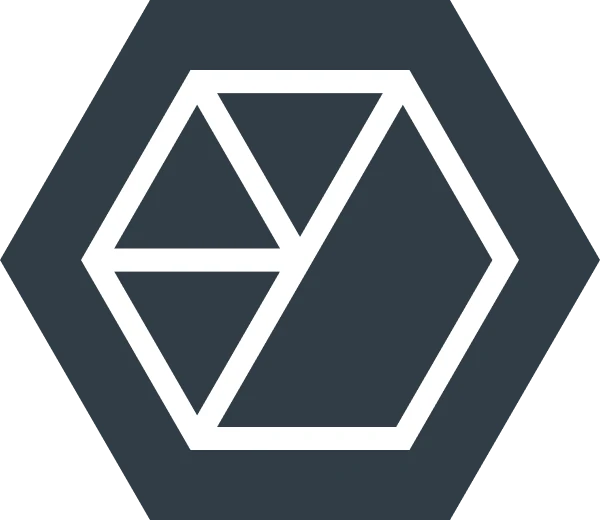
About the author
Beekeeper
We make frontline lives easier, work safer, and teams more connected so businesses can reach new heights. At Beekeeper, we’re dedicated to making frontline lives easier by connecting workers with the tools, support, and information they need to feel valued, do their best work, and drive the business forward.