When equipment breaks down or doesn’t function properly, it can cause significant disruptions or even halt production. Creating a preventative maintenance checklist helps minimize those failures and creates a safer, more productive work environment.
Learn how preventative maintenance can boost equipment uptime by 20%
At Beekeeper, we’ve worked with many frontline organizations looking to improve their internal communication strategy. We’ve seen how creating checklists, especially for manufacturing organizations, is an essential element of Frontline Success.
One of the Frontline Trends we’re seeing is more organizations making an effort to digitize workflows. We’re predicting that organizations will embrace a more digitized approach to creating, distributing, tracking, and analyzing checklists, particularly when it comes to preventative maintenance.
In this in-depth guide, we’ll be looking at:
- What is a preventative maintenance checklist
- The benefits of having a maintenance equipment checklist
- How to create an equipment maintenance checklist
- Best practices for creating a preventative maintenance checklist
Let’s begin.
What Is A Preventive Maintenance Checklist?
A preventative maintenance checklist is an essential tool used by organizations to ensure that equipment, machinery, and facilities are operating at optimal levels. Essentially, it is a list of tasks that need to be completed regularly to:
- Prevent breakdowns
- Ensure safety
- Prolong the lifespan of equipment
A preventative maintenance checklist typically includes a range of tasks such as equipment inspections, cleaning, lubrication, repairs, and replacements. An equipment maintenance checklist is usually completed on a regular basis, like monthly, quarterly, or annually, depending on the specific needs of the equipment in question.
The purpose of a maintenance equipment checklist is to help organizations avoid costly breakdowns and repairs, reduce downtime, and maximize productivity.
5 Benefits of Using Preventative Maintenance Checklists
The benefits of implementing a preventative maintenance checklists include:
1. Fewer Costly Breakdowns and Repairs
By regularly inspecting and maintaining equipment, organizations can detect potential issues before they lead to major breakdowns or safety hazards. This not only reduces the risk of costly repairs but also helps businesses avoid downtime, which can be a significant drain on productivity and profitability.
2. Maximized Lifespan of Equipment
By keeping equipment in good working condition, organizations can prolong its lifespan and reduce the need to replace it prematurely. This can result in significant cost savings over time, as organizations can avoid the expense of purchasing new equipment and can continue to operate efficiently with their existing equipment.
3. Safer Workplace
An equipment maintenance checklist can also help organizations comply with safety regulations and ensure that their equipment is operating safely for their workers. By conducting regular safety inspections and maintenance, businesses can identify and address safety hazards, reducing the risk of workplace accidents and injuries. This not only protects employees but also helps businesses avoid costly legal fees and fines associated with non-compliance with safety regulations.
4. Improved Productivity
By keeping equipment in good working condition, organizations can avoid unexpected downtime and ensure that it continues to operate at optimal levels. This can result in increased efficiency and productivity, as organizations can operate more smoothly and with fewer interruptions.
5. More Profit
Finally, preventative maintenance checklists can help organizations improve their overall operations and profitability. By identifying and addressing potential issues before they become major problems, organizations can reduce costs, increase productivity, and improve safety in the workplace. This can help businesses to operate more efficiently and effectively overall, leading to increased profitability and success over time.
3 Key Components of a Preventative Maintenance Checklist
So what makes a preventative checklist successful?
Let’s look at three main elements:
1. Equipment Inspection and Maintenance
Regular equipment inspections and maintenance can help prevent breakdowns, reduce downtime, and extend the lifespan of the equipment. Maintenance tasks can include cleaning, lubrication, adjusting, and replacing worn parts. By performing these tasks regularly, the equipment can function at optimal levels and reduce the risk of failure. In addition, inspections can identify potential issues before they become major problems, allowing for timely repair or replacement.
The schedule for equipment inspections is usually based on the type of equipment and its usage. Inspections should include a thorough examination of all parts and components, including electrical systems, mechanical systems, and structural elements. Maintenance tasks should be performed according to the manufacturer’s recommendations and documented for future reference. By implementing a comprehensive equipment maintenance checklist, companies can reduce costs associated with repairs and replacements and ensure that equipment is operating safely and efficiently.
2. Safety Inspection and Maintenance
Ensuring that equipment and machinery are operating safely is essential to protecting frontline workers and preventing accidents in the workplace. By including safety inspections and maintenance in a preventative maintenance checklist, companies can reduce the risk of injury or harm to employees and maintain compliance with safety regulations.
Inspection checklists typically include a thorough examination of all safety components, including guards, shields, safety switches, and emergency stop buttons. Additionally, electrical systems should be inspected for any potential hazards, such as frayed wires or loose connections. Part of safety inspection and maintenance can also include regular cleaning, lubrication, adjustment, and replacement of worn parts.
A preventative maintenance checklist can also include follow-up action steps that direct employees on how to properly report safety issues once they’re detected.
3. Records and Documentation
Proper documentation is essential for:
- keeping track of equipment maintenance schedules
- identifying potential problems
- ensuring that all maintenance tasks are completed on time
Without proper documentation, it can be challenging to keep track of when maintenance tasks were last performed, which can lead to missed maintenance opportunities and equipment failure.
The documentation process should begin with the creation of a maintenance log. One potential preventative maintenance checklist template could include the:
- Equipment being maintained
- Date and time of maintenance
- Name of the technician responsible for the task
Pro Tip: Digitizing a maintenance log using a frontline success system like Beekeeper allows for real-time updates and keeps records easily accessible to all members of the maintenance team.
It’s also important to maintain records of equipment performance.
This can include data such as the:
- Frequency of breakdowns
- Severity of those breakdowns
- Expected cost of repairs
By analyzing this data, maintenance teams can identify patterns in equipment failure and take preventative measures to avoid future issues.
Another important element of documentation in preventative maintenance is the creation of work orders. Work orders are used to assign maintenance tasks to specific technicians and ensure that all necessary materials and tools are available.
Work orders should include the:
- Description of the task
- Equipment involved
- Any safety precautions that need to be taken
Maintaining accurate records of any repairs or replacements that are made during preventative maintenance helps track the lifespan of equipment and identify when it is time for a replacement. It can also be used to identify potential issues with specific types of equipment and inform future equipment purchasing decisions.
4 Steps to Developing a Preventative Maintenance Checklist
Now that we’ve looked at the elements of a successful maintenance equipment checklist, how can organizations start developing their own? Here are 4 steps to consider:
- Identify Critical Equipment and Safety Hazards
To identify critical equipment, organizations should conduct a thorough review of their operations and identify the machinery, systems, and equipment that are most critical to their business. This may include equipment that is:
- Used frequently
- Used in high-risk processes
- Expensive to repair or replace
Then, organizations can begin to develop a preventative maintenance checklist that takes into consideration:
- The specific needs of each piece of equipment
- Potential safety hazards like exposed wires, slippery floors, or hazardous chemicals
- Providing safety equipment like goggles, suits, and gloves
- Modifying equipment or processes to reduce safety risks
- Prioritize Maintenance Tasks
Prioritizing maintenance tasks involves identifying the maintenance activities that require immediate attention and those that can be deferred to a later date.
This helps organizations:
- Allocate their resources effectively
- Reduce downtime
- Improve overall operational efficiency
One way to prioritize maintenance tasks is to categorize them based on their level of importance. Tasks that are critical to the operation of the organization or have a high impact on safety should be given the highest priority. These tasks could include the inspection, testing, and repair of critical equipment, safety systems, and emergency generators.
Tasks that are important but not critical should be given a lower priority. These tasks may include routine maintenance activities like lubrication, cleaning, and calibration of equipment. These tasks may be essential, but they can be deferred to a later date if necessary.
- Assign Responsibility for Maintenance Tasks
Assigning responsibility for maintenance tasks identifies the individuals or teams responsible for performing the maintenance activities and ensures that they have the necessary skills, knowledge, and resources to complete the tasks effectively.
Assigning responsibility for maintenance tasks begins with identifying the equipment or systems that require maintenance and the specific tasks that need to be performed. Then, the responsibility for each task should be assigned to an individual or team based on expertise and availability.
In some cases, maintenance tasks may be assigned to a dedicated maintenance team or department. This team would be responsible for ensuring that all maintenance tasks are completed in a timely and effective manner. Alternatively, maintenance tasks may be assigned to the individuals or teams that operate the equipment or systems, which ensures that those who are most familiar with the equipment are responsible for maintaining it.
Assigning responsibility for maintenance tasks should also include providing the necessary training and resources. This may include providing training on specific maintenance procedures or providing access to maintenance manuals and other resources.
Pro Tip: Beekeeper has partnered with mobile-first microlearning platform EduMe to help make frontline training programs accessible and fun. For example, with Beekeeper, it’s easy for managers to create micro-training programs on specific maintenance procedures.
- Schedule Preventative Maintenance Activities
Scheduling preventative maintenance activities involves determining the frequency of maintenance tasks and creating a schedule that ensures these activities are completed on time.
To create a schedule for preventative maintenance activities:
- Identify the equipment or systems that require maintenance and the specific tasks that need to be performed. Based on the manufacturer’s recommendations, industry standards, and previous maintenance records, organizations can determine the ideal frequency of maintenance tasks.
- Create a schedule that outlines when each task needs to be completed. The schedule should take into account the availability of personnel, equipment, and resources required.
- Prioritize maintenance tasks based on the importance and the impact they may have on the equipment’s performance. For example, tasks that are critical to the equipment’s operation or safety should be given higher priority than tasks that are less critical.
- Review and adjust the preventative maintenance schedule regularly by monitoring the equipment’s performance, reviewing maintenance records, and making changes to the schedule as necessary.
Best Practices for Preventative Maintenance
Here are three more best practices to keep in mind while creating your organization’s preventative maintenance checklists.
- Regular Inspections and Maintenance
Regular inspections involve routine checks of equipment and systems to identify potential issues early, while maintenance involves performing specific tasks to keep equipment and systems in optimal condition and prevent breakdowns. Regular inspections and maintenance can also help to ensure that equipment is operating safely and efficiently, reducing the risk of accidents or injuries.
Preventative maintenance checklists for inspections may include checks for wear and tear, leaks, corrosion, and other signs of damage or deterioration. Maintenance checklists could include tasks like cleaning, lubrication, and replacing worn or damaged parts. While workers may already be familiar with these tasks and perform them regularly, referring to a checklist helps reduce human error and accommodate less experienced or new employees.
- Conducting Inspections and Maintenance During Off-Peak Seasons
Conducting inspections and maintenance during off-peak seasons can help organizations avoid disruptions to their operations. During off-peak seasons, equipment and systems may not be used as frequently, providing an opportunity to perform maintenance and repairs without impacting productivity.
By conducting inspections and maintenance during off-peak seasons, organizations can identify and address issues before they escalate, reducing the need for emergency repairs during peak seasons when equipment and systems are in high demand.
Off-peak seasons also provide an opportunity to perform more extensive maintenance tasks that may require longer periods of downtime. For example, equipment may need to be taken offline for maintenance and repairs that cannot be performed while in use. By scheduling these tasks during off-peak seasons, organizations can minimize the impact on productivity and reduce the risk of disruptions during peak seasons.
- Utilizing Technology and Automation
Technology and automation help organizations:
- Monitor equipment and systems in real-time
- Identify issues that might get overlooked
- Automate routine maintenance tasks
One way organizations can utilize technology and automation is by implementing sensors and monitoring systems to track the performance of equipment and systems. These sensors can detect changes in temperature, pressure, vibration, and other key indicators, and alert maintenance teams to potential issues.
Another way is automating routine maintenance tasks. For example, automated lubrication systems can ensure that equipment is properly lubricated without the need for manual intervention. This can help to extend the lifespan of equipment and reduce the risk of breakdowns due to improper lubrication.
Organizations can also use predictive maintenance software to analyze data from sensors and other sources to predict when maintenance tasks will be needed. This can help organizations to schedule maintenance tasks more efficiently and reduce the risk of unexpected breakdowns.
Mobile communication apps like Beekeeper can help:
- Give frontline workers real-time access to preventative maintenance checklists
- Allow managers to track progress and analyze results
- Create training programs for improving skills and knowledge in preventative maintenance
Creating an Effective Preventative Maintenance Checklist: Key Takeaways
Preventative maintenance checklists are tools used by organizations to ensure that equipment, machinery, and facilities are operating at optimal levels. These checklists help organizations avoid costly breakdowns and repairs, reduce downtime, and maximize productivity.
The benefits of using preventative maintenance checklists include:
- Fewer breakdowns and repairs
- Maximizing the lifespan of equipment
- Creating a safer workplace
- Improving productivity
- Increasing profits
Developing a preventative maintenance checklist involves:
- Identifying critical equipment and safety hazards
- Prioritizing maintenance tasks
- Assigning responsibility for maintenance tasks
- Scheduling preventative maintenance activities
Mobile communication apps like Beekeeper can give frontline workers real-time access to preventative maintenance checklists, allow managers to track progress and analyze results, and create training programs for improving skills and knowledge in preventative maintenance.
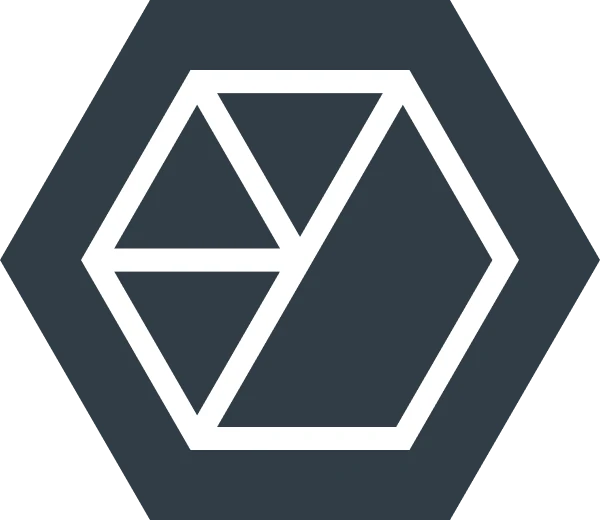
About the author
Beekeeper
We make frontline lives easier, work safer, and teams more connected so businesses can reach new heights. At Beekeeper, we’re dedicated to making frontline lives easier by connecting workers with the tools, support, and information they need to feel valued, do their best work, and drive the business forward.